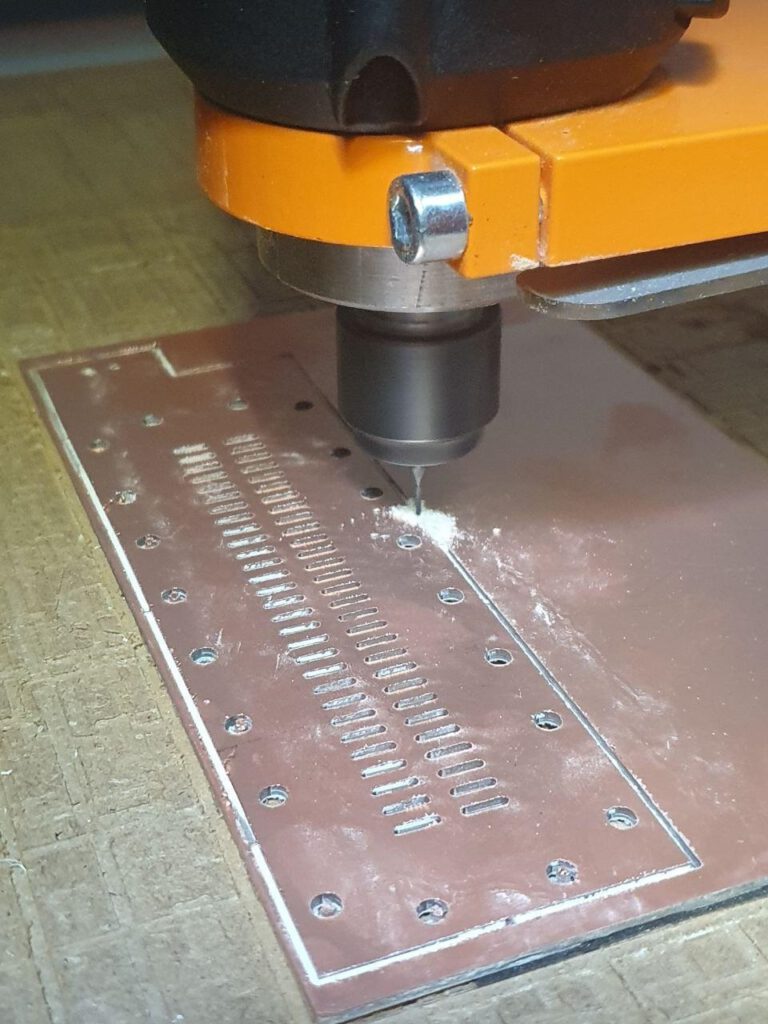
We thought this would be easy: milling the conductor plates according to Burghard’s design to produce the flowfield and the open electrode. We gave a set of milling cutters to Frauke from the FabLab and were excited to receive the cut parts within the next few days. Instead, we received news from the FabLab: all our cutters are gone, the plates still there. Well, we needed to check back with Burghard: turns out we need diamond cutters. Leander ordered three of them. Well, two are gone, one left. Ok, let’s get this straight now – carefully cutting with exactly the settings that Burghard used (LINK). Our third cutter survives. And. Does. The. Job. 😍
OK, so we’ve got five plates, two flowfields and three open electrodes. Amazingly enough, I learn that the FabLab crew already printed some sealings. They, however, did not use the filament that Burghard used but used some TPU which they have already got. Well, the test for gas tightness of those is still pending.
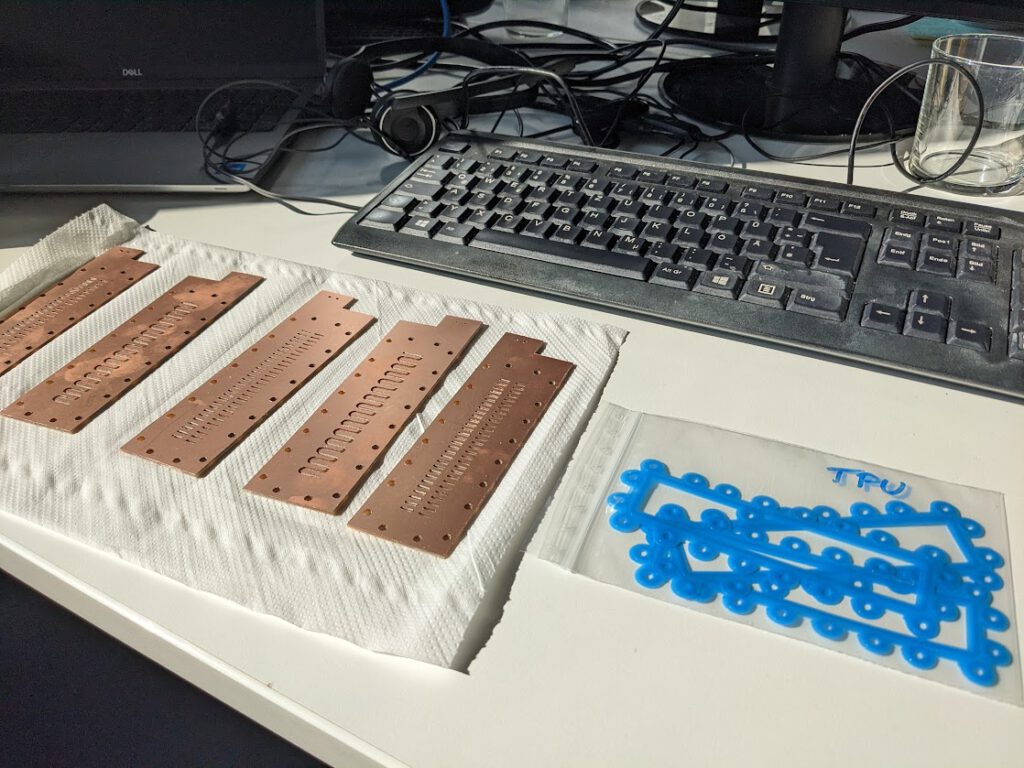
Before we can test this, we still need to galvanize our plates. In one of our last meetings, Roland just incidentially mentioned that before gold-plating, we need to nickel-plate the conductor plates. Since we want OFC assembly to be accessible for as many people as possible, we do our best to find electroplating equipment that can easily be acquired by private persons. With nickel electrolytes only being shipped to corporate customers by some providers this seemed tricky at first. However, we found a retailer that ships to everyone and decided to order the following items: electroplating set, gold electrolyte, nickel electrolyte.
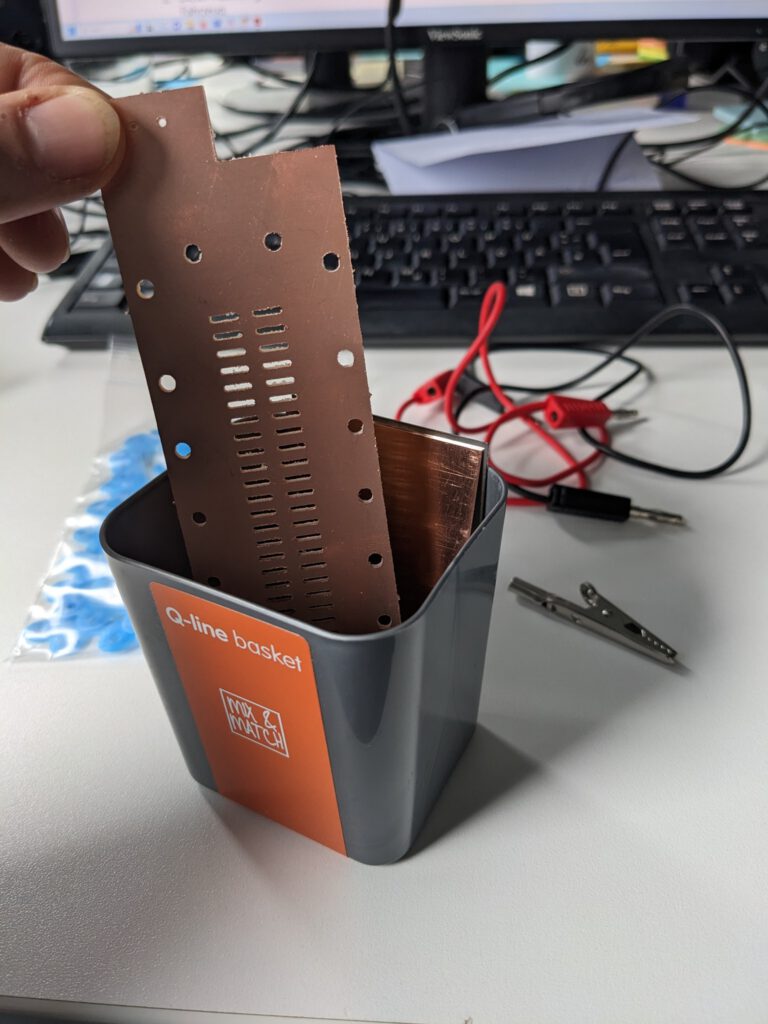
All items arrived within a few days after ordering. However, we soon realized that the bath of the electroplating set is not ideal to say the least. Well, either we build ourselves another bath that fits the entire plates or we need to galvanize one half followed by the other. 😅 Well, let’s see what Roland, our electroplating expert will say at the next meeting.