Livia and Roland are on vacation; so there is only a small Open Fuel Cell team meeting. We meet at the Chair of Energy Technology.
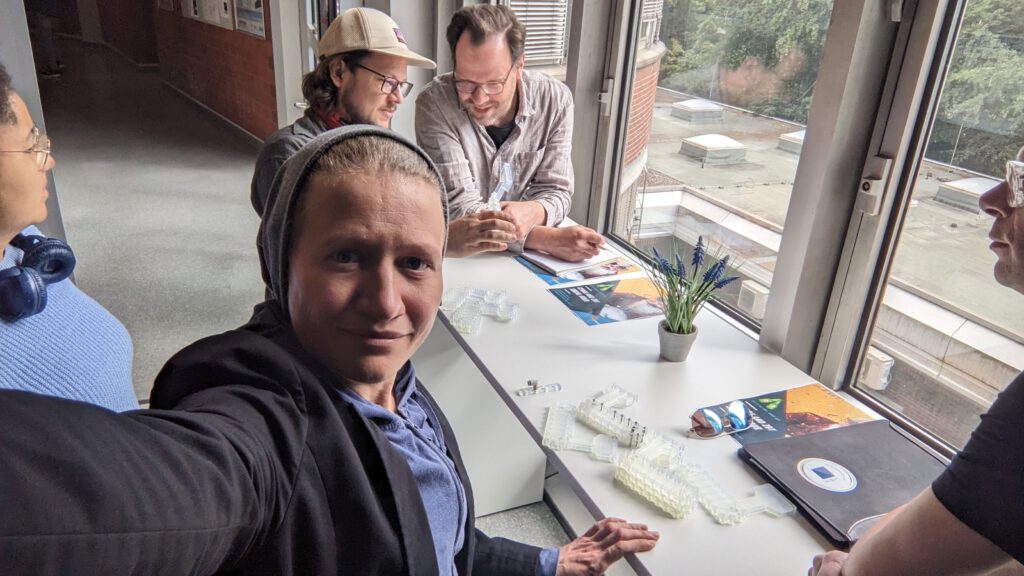
Leander reports about the experiences he made when he tried to print more end plates using SLA. He had problems with the threads, which were somehow always crap. He solved it in the end with a testing piece on which he could test the different pressure parameters.
We discuss that the last step which need to be undertaken to assemble a first cell with all the parts which we manufactured during the last months. Last meeting we finally managed to electroplate the electrode and flowfield with a Nickel electrolyte. So now, all we need to do is to electroplate these parts with gold.
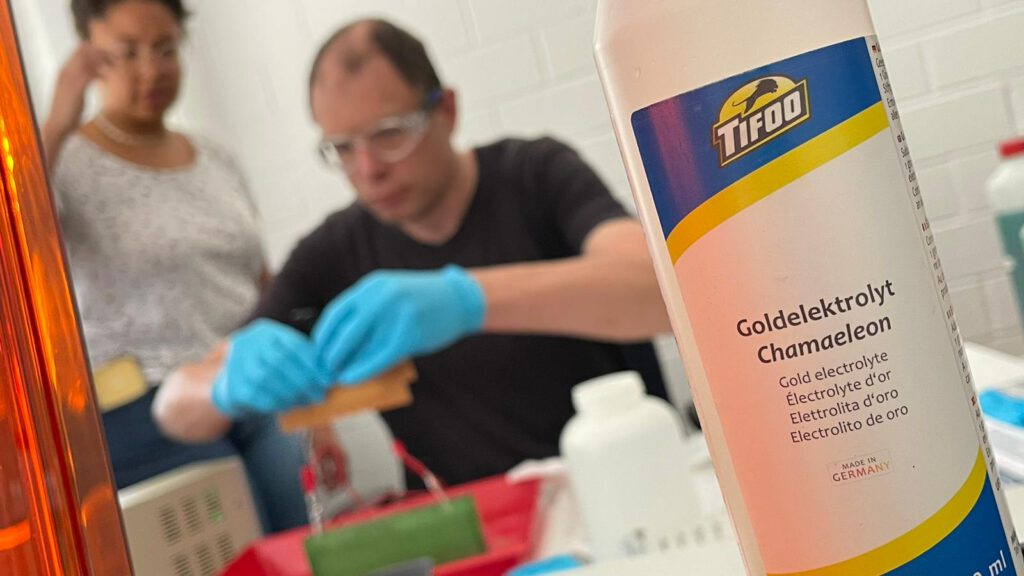
We walk to the room which Leander and Livia called 3D-FabLab 2.0. Alexandra sets up the electroplating set. This time it’s all going more smoothly. Burghard connects the stainless steel electrode in the bath with the red cables and the black cable clamp to the nickel plated pieces. With 3 V and 0.6 A we see bubbles and it takes about a minute until we clearly see gold deposition and declare the job done.
We should now have all parts together to build our first “self-made” cell. That is, of course, except for the MEA, which will be a topic on its own. The MEA is assembled using professional equipment at the ZBT and we briefly discuss how we could also make manufacturing of the MEA as transparent and accessible as possible. Burghard will have a look at potential online distributors for MEA/GDL material and share his findings with us.
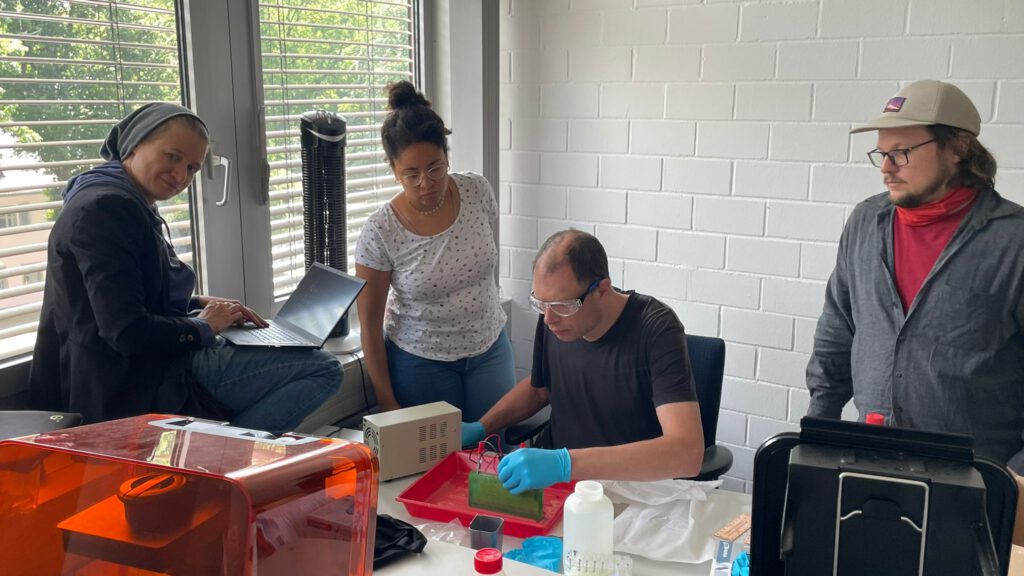
Alexandra and Burghard report that they are currently testing gas tightness of the original fuel cell when powered with the Horizon Hydrosticks. If the original plate with the filament-printed end plates does not turn out to be gas tight, Burghard wants to test the greentech filament, about which we reported in a previous meeting (Link). They will report about the results of their testing in the next couple of days.
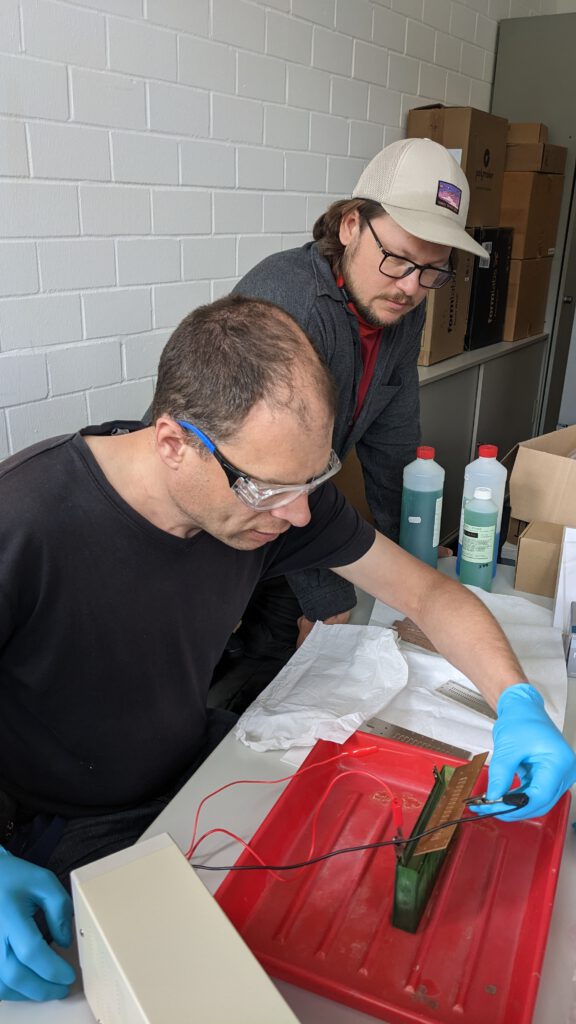
So for the next meeting we can plan to finally assemble our first “own” cell. It’ll be interesting to see whether the sealings which we printed in the FabLab using TPU instead of recreus filaflex 70A.
Burghard reports that next week, school students will visit the ZBT and he will show some OFCs in action. We discuss if we want to exhibit and demonstrated the OFC at the Duisburg Maker Day in September. Of course we do! We discuss that we want to show the whole assembly line, potentially also assemble cell live and operate the cell. For operation, we would love to really power something that is clearly visible to visitors. However, since we only expect about 0.4 V as output of one OFC, we want to test if we could use a step up converter to power an LED. If that won’t work we can at least demonstrate a U-I characteristic curve.